+Garment Mending Types+
+check back often as these examples are expanded upon and updated+
BOOKS CLOSED UNTIL 9/9/2025
+
BOOKS CLOSED UNTIL 9/9/2025 +
finished machine darning with contrast threads on vintage Wrangler denim by Rae
+Visible Machine Mending Method+
The above is a classic example of a machine darning method used to create a unique visible mending look. A patch is added to the interior of the garment and repaired by stitching repeatedly over the torn area vertically and horizontally to reinforce the area and mimic a woven pattern. This can be done with any color of patch underneath and any thread color.
As you can see in the photo above, the under patch is a faint baby blue color and the threads are a golden hue to match the original stitching on these vintage Wranglers.
HOPES utilizes threads made in Germany out of 100% rPET recycled plastic bottles for machine mending and donated/deadstock fabrics for patching.
finished machine darning with matching threads on vintage Levi’s denim by Rae
+NEARLY Invisible Machine Mending Method+
The above is another classic example of the machine darning method used to create a more subtle and seamless look. Often times denim needs to be patched in high abrasion areas like knees, inseam, crotch, hems and pockets.
For this restoration, Rae used genuine Levi denim to patch the gap. To stay true to the HOPES style of organized chaos mending and stitching, they set the weave of the patch on grain to prevent stretching, but flipped the direction of the twill to balance the left and right hand changes that the jeans already have. If this sounds confusing, take a look at the diagonal lines in the fabric on the waistband, yoke, pocket and leg to see the directional changes of the twill.
HOPES utilizes threads made in Germany out of 100% rPET recycled plastic bottles for machine mending and donated/dead-stock fabrics for patching.
Nearly Invisible Machine Darning on a distressed 100% cotton vintage t-shirt by Rae
+Nearly Invisible Machine Darning for Knits+
This method for fixing thrashed and damaged knitwear is a delicate multi-step process. Rae has developed this method in the HOPEStudio (mainly) to restore t-shirts to their former glory, but this method can be used for most fine knits. The process itself involves matching a similar weight knit, multiple-thread colors and a stabilizer to prevent stretching while being stitched. The method is suitable for most knitwear garments with holes—threadbare garments could also use this treatment on a case by case basis.
in progress hand sashiko-inspired method on vintage Cadillac denim by Rae
+Sashiko and Boro-inspired Method+
The sashiko method of stitching is widely believed to have been created in the Edo period (1603-1867) in Japan, though it could have been earlier. The process initially was created out of necessity but ultimately grew to the art form that it is today, with sewists creating boro inspired pieces in the name of sustainability.
The continuous process of sashiko stitching is known as boro when it is layered continuously. Think of sashiko as the thread and action of stitching and boro as a finished piece of fabric or a garment with the stitching embedded in it. It is not uncommon for the two terms to be used interchangeably today because there is not a lot of documentation for how these methods were initially developed. Sashiko was traditionally done on dark indigo fabrics with white/off-white cotton threads by those who were impoverished and utilized only what they had on hand. The people using sashiko also took great care in mending the items that they wore everyday and passing them down generation to generation.
Sashiko and boro have stood the test of time for sustainability practices and in recent years have become increasingly popular among the sustainable fashion community, designers and artisans. The best part of sashiko and boro is that it can be built up and layered repeatedly to create garments as unique as the people wearing and making them, all while adding strength to the garments.
HOPES utilizes 100% cotton threads from Japan for the sashiko method and honors the tradition of utilizing every scrap of fabric available—the idea of “waste not, want not” comes to mind.
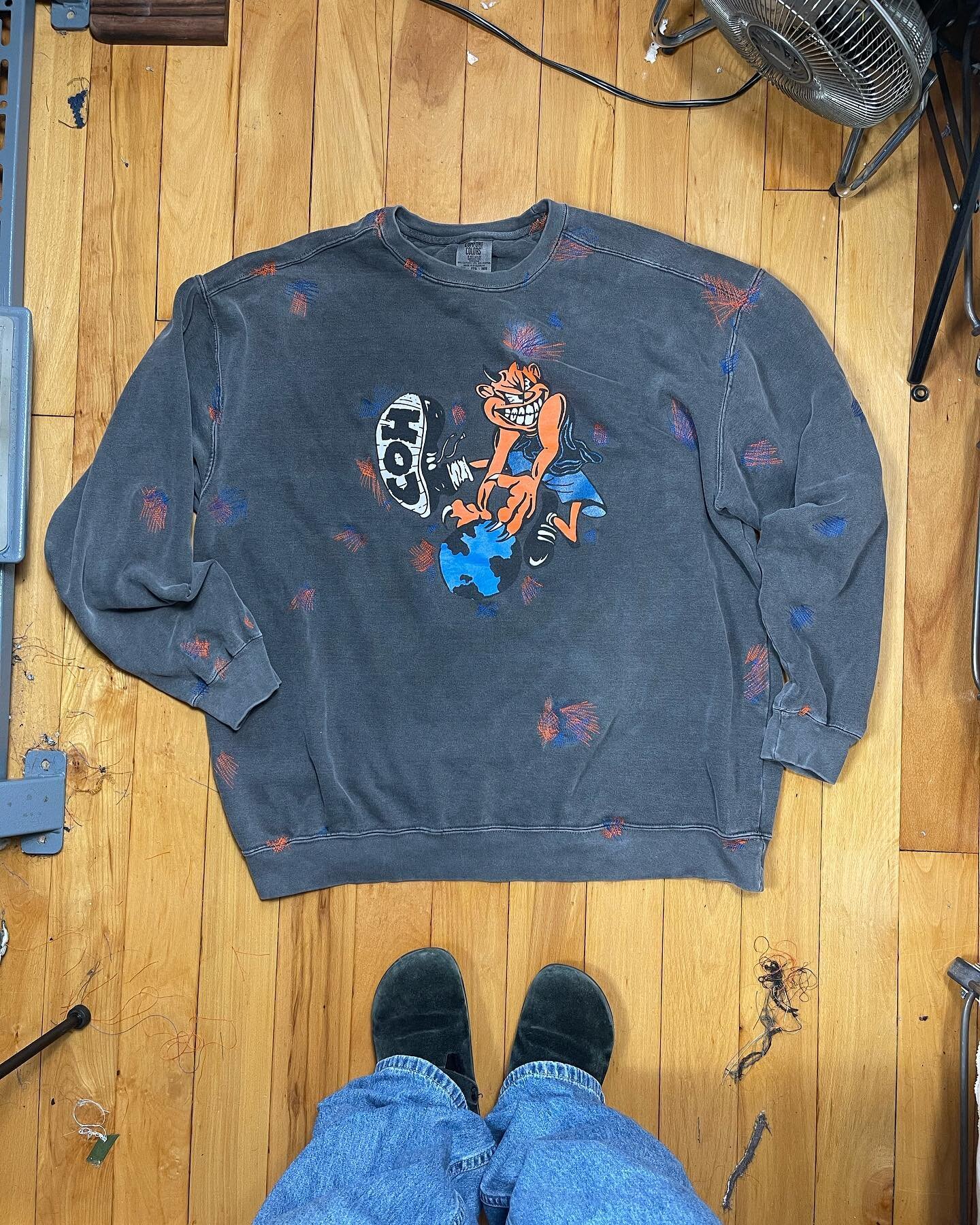
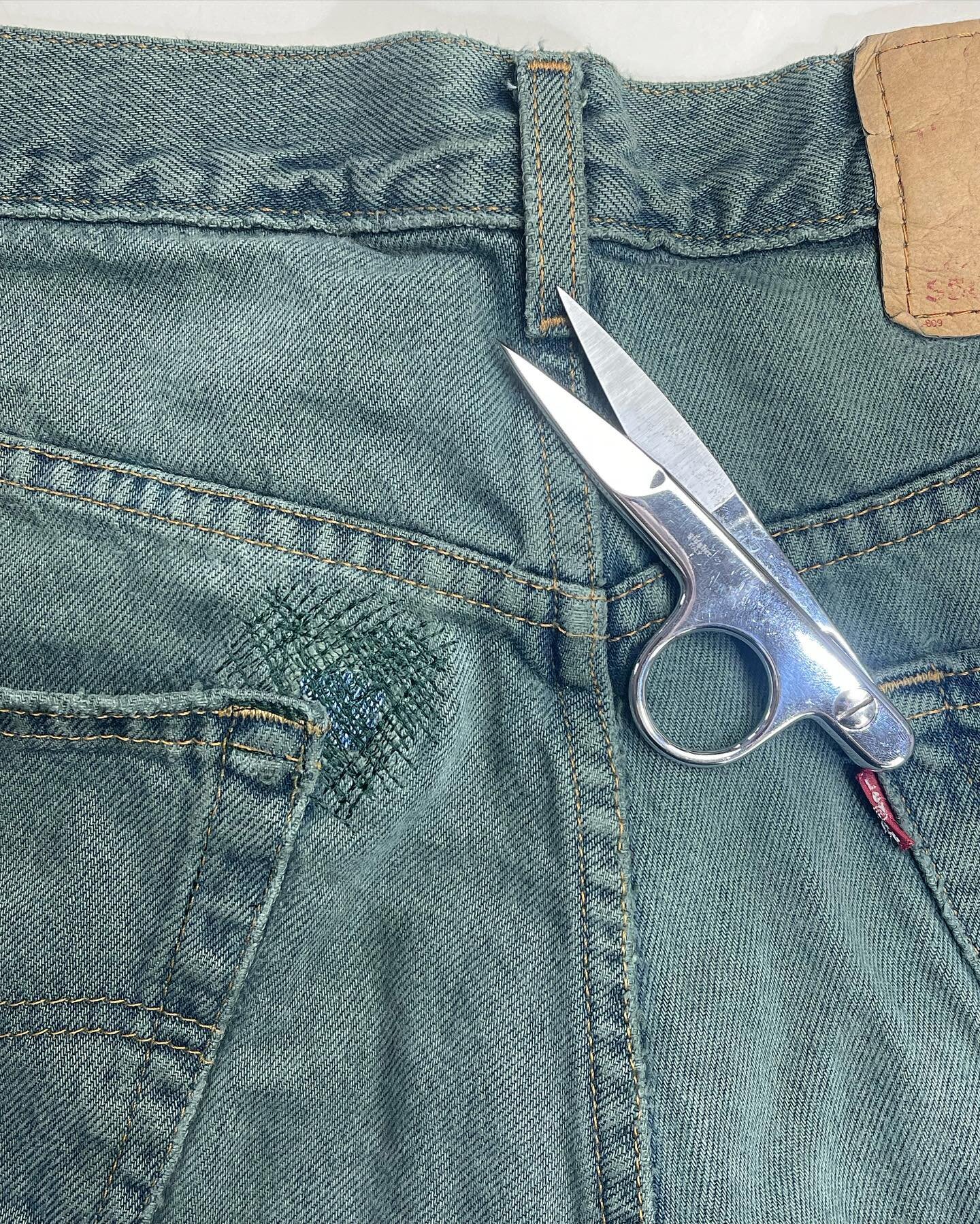
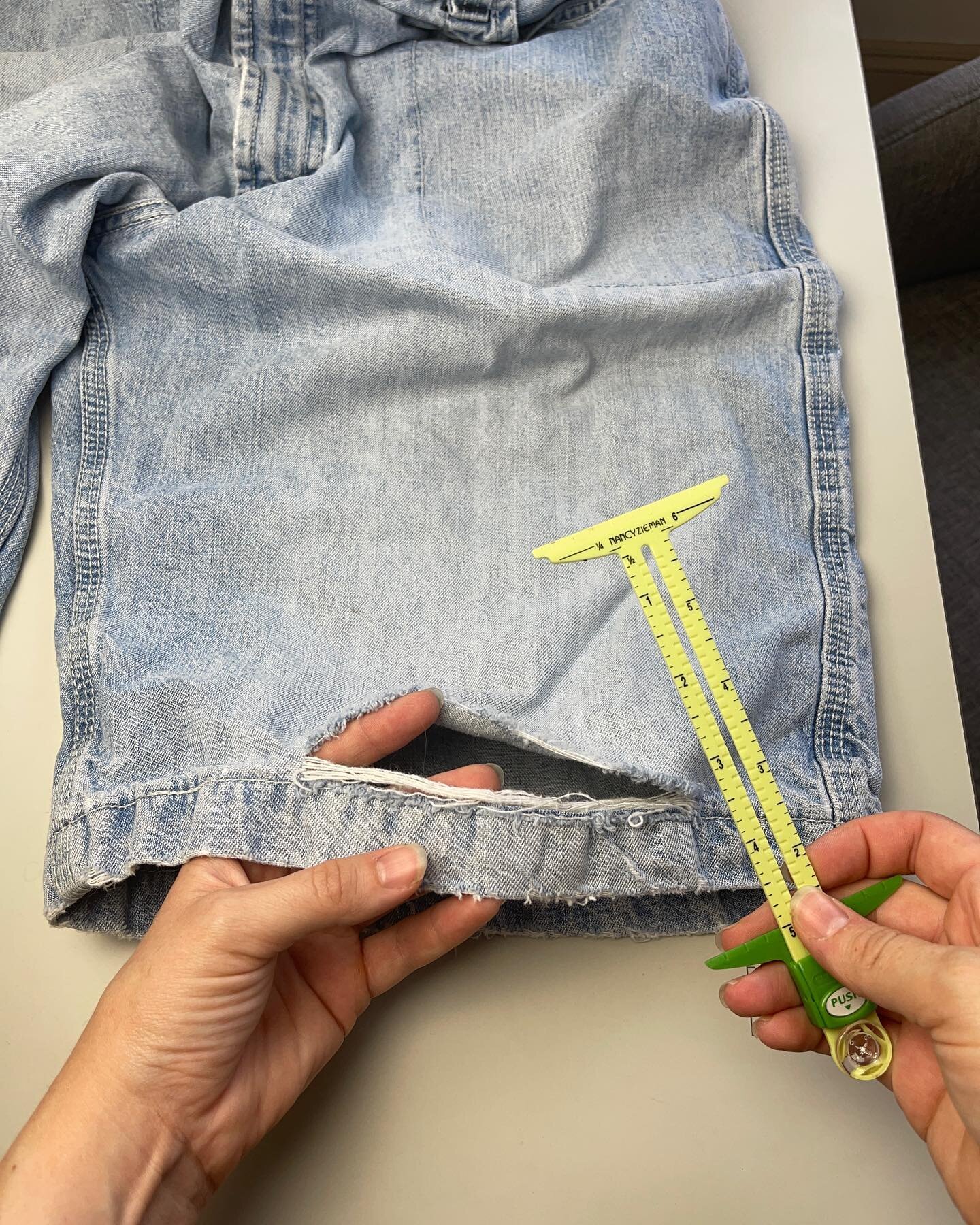